The Importance of Tool Management for Job Sites: How Innovative Solutions Like Toolcase Prevent Loss and Increase Efficiency
- Smart Toolcase
- Feb 24
- 3 min read
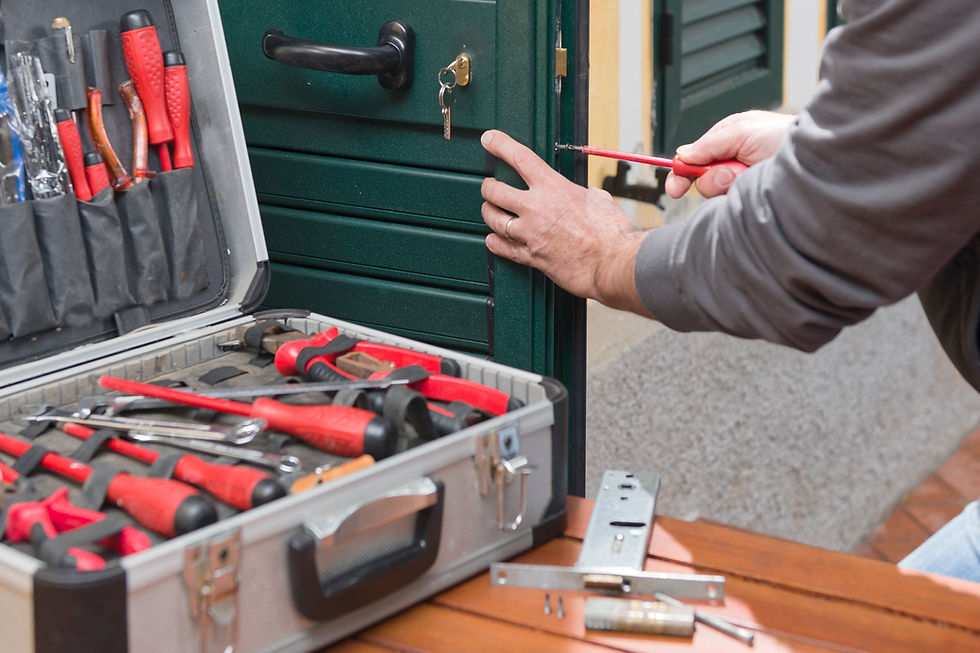
Effective tool management is a critical aspect of maintaining productivity, reducing costs, and ensuring smooth operations on job sites. In an environment where time is money, misplaced or stolen tools can lead to costly project delays, increased expenses, and compromised safety. Traditional methods of managing tools, such as manual tracking, barcode scanning, or spreadsheets, are inefficient and prone to human error. This is where innovative solutions like Toolcase offer a game-changing approach to tool management, using advanced RFID technology and AI-driven insights to enhance job site efficiency and prevent tool loss or theft.
Why Tool Management is Critical for Job Site Success
Tool loss or misplacement on job sites is a common problem that affects overall productivity and profitability. Every missing tool translates into wasted time, increased costs, and potential project delays. Consider the impact of these key challenges:
Lost Productivity: Workers often spend valuable time searching for misplaced tools, which disrupts workflow and results in lost productivity. According to industry studies, the cost of searching for a single misplaced tool can far exceed its replacement cost due to downtime.
Increased Costs: Frequent tool replacements due to loss or theft can accumulate into significant expenses. A misplaced $80 tool, for example, could cost a construction company several hundred dollars in lost productivity and replacement costs.
Project Delays: Missing tools can delay critical tasks and extend project timelines. Delays can lead to penalties, loss of future contracts, and a damaged reliability reputation.
Security Risks: Construction sites are vulnerable to theft, especially during off-hours. Without effective tool management, high-value equipment becomes an easy target.
Innovative tool management solutions like Toolcase address these issues through real-time tracking, automated alerts, and a streamlined inventory management system. By leveraging RFID technology and AI-powered insights, Toolcase provides a more efficient and secure approach to managing tools on job sites.
How Toolcase Revolutionizes Tool Management
Toolcase offers a comprehensive solution for tracking, managing, and securing tools on job sites. It uses a combination of RFID technology, AI-driven insights, and a user-friendly smartphone application. Here’s how Toolcase transforms tool management:
RFID-Based Tracking: Each tool is equipped with an RFID tag that transmits a unique identifier to an RFID reader placed inside the toolbox or work vehicle. The RFID reader continuously scans tools as they enter or exit the designated storage area, updating the digital inventory in real time.
Dynamic Triangulation Technology: Unlike basic RFID systems, Toolcase uses dynamic triangulation to determine the precise location of each tagged tool. By constantly pinging RFID tags and analyzing their relative positions, Toolcase provides real-time tracking down to 5mm, allowing workers to quickly retrieve misplaced tools.
Automated Alerts for Missing Tools: Toolcase’s smartphone application sends automated alerts when tools are missing from the toolbox or storage area. Users receive notifications before leaving the job site, reducing the risk of forgetting or misplaced tools.
AI-Enhanced Inventory Management: Toolcase incorporates AI technology to automate inventory management tasks. The AI-powered app recognizes and categorizes tools based on a photo, reducing manual data entry. Over time, the system learns from usage patterns, improving its accuracy at identifying tools.
Scheduled and Location-Based Scanning: The system offers three scanning and alert triggers: manual scans, scheduled scans at specific intervals, and location-based scans that detect tool movement when the RFID reader’s geolocation changes. This ensures that any missing tools are detected before leaving the job site.
Compatibility with Various RFID Tags: Toolcase supports both active and passive RFID tags, making it suitable for a wide range of job site environments. Active RFID tags offer long-range tracking for large sites, while passive tags provide a cost-effective solution for smaller workspaces.
By providing real-time tracking, automated alerts, and AI-driven insights, Toolcase simplifies tool management, improves job site efficiency, and reduces tool loss or theft risk.
Embracing the Future of Tool Management
In today’s fast-paced construction and industrial environments, effective tool management is essential for maintaining productivity, reducing costs, and ensuring project success. Traditional methods of managing tools are often inefficient and prone to errors, leading to lost productivity and increased expenses. Toolcase offers a smarter, more efficient solution by combining RFID technology, dynamic triangulation, and AI-driven insights to enhance tool tracking, inventory management, and job site security.
With Toolcase, companies can automate tool tracking, receive real-time alerts for missing tools, and access precise location data for each tool, ensuring that every piece of equipment is accounted for before leaving the job site. This innovative approach to tool management saves time, reduces costs, and improves overall efficiency, making it an invaluable investment for any job site looking to enhance operations.
Invest in a smarter, more secure future for your job site with Toolcase – a game-changing solution for tool management and inventory control.
Comments