Toolcase Smart RFID System: Reliable Tool Tracking for Mobile Job Sites
- Smart Toolcase
- May 11
- 4 min read
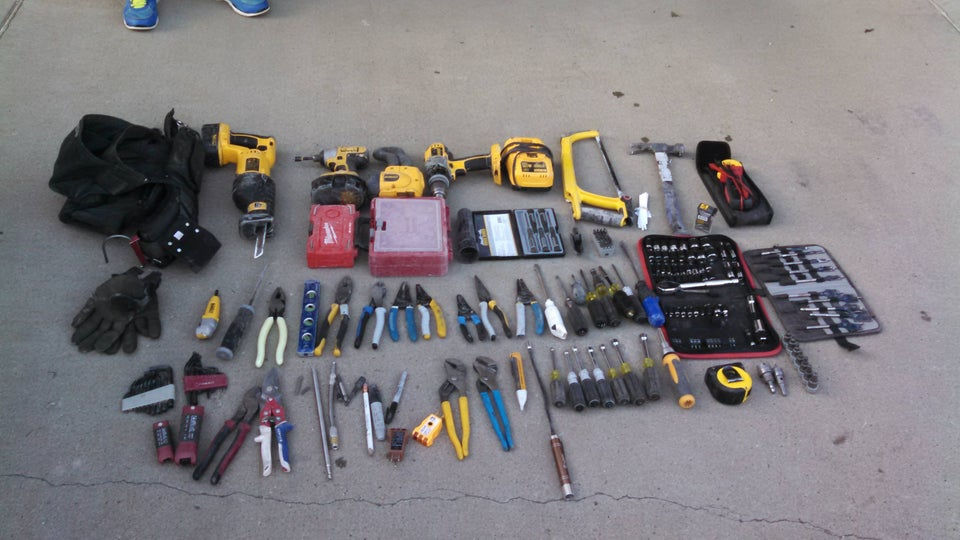
Tool loss is one of the most common and costly problems on mobile job sites. Teams work in motion, equipment is moved between trucks, tool bags, and temporary workstations, and the pace of operations makes manual tracking unreliable. Misplaced or forgotten tools result in wasted time, duplicate purchases, and delays in completing tasks. Toolcase addresses these challenges with a compact, intelligent system that integrates RFID tracking, Bluetooth connectivity, and AI-driven inventory management. It works with both passive and active tags and provides real-time alerts and exact location data. This system simplifies inventory, prevents accidental losses, and adapts to a wide range of job site conditions.
RFID Tracking Built for Accuracy and Durability
Toolcase features a universal RFID reader that supports both active and passive tags. It scans tools automatically and detects their presence inside toolboxes, work vans, or containers. Passive tags provide a short scanning range and are ideal for smaller environments. Active tags have a larger range and are more suitable for tracking tools across larger work zones, storage trailers, or multiple vehicles. Both types work seamlessly with the Toolcase.
The RFID reader connects to a smartphone through Bluetooth and communicates with the Toolcase mobile app. Once connected, the reader constantly monitors the surrounding area for RFID signals. It has the ability to perform dynamic triangulation, which uses signal data from multiple angles to determine the exact location of each tool. This allows workers to locate items even when buried under other equipment or stored in hard-to-reach places. The system has location accuracy up to 5 mm.
The Toolcase device housing is waterproof, dustproof, and shock-resistant. It is designed to operate in harsh job site environments and withstand rough handling. The internal battery lasts up to 72 hours without recharging. A built-in power bank allows the device to recharge smartphones and small electronics while in use. This makes Toolcase a self-contained solution for demanding conditions without external infrastructure or dependencies.
Real-Time Alerts and Checks for Missing Tools
Toolcase includes three scanning modes for detecting missing equipment. The first is a manual scan activated through the device’s Quick Check button. This lets the worker instantly verify that all tools are inside the case or container before moving to another location. The result is shown through lights on the device or through the mobile app. This feature alone prevents the most common type of tool loss, during site transitions.
The second mode is scheduled scanning. Users can set specific times for the system to run automatic checks, ensuring regular inventory control without requiring worker involvement. This is useful during shift changes or site departures when memory-based checks are unreliable.
The third mode is triggered by movement. When the Toolcase detects that its physical location has changed—such as being lifted, loaded, or carried to another zone, it automatically runs a full scan. If any assigned tools are missing from the scanned inventory, an alert is sent to the user’s smartphone. This scanning logic guarantees tools are not forgotten or stolen during transport. Even if the user is already on the way to a new job site, Toolcase will notify them in real time.
The alert system does not depend on internet access. All RFID data is stored and processed on the device and smartphone app. Notifications are instant, reliable, and visible even when connectivity is limited. This design allows Toolcase to operate effectively across a wide range of job environments.
AI-Powered Inventory for Organized Tool Tracking
Toolcase features a built-in AI system that improves inventory control. Once the RFID reader is connected to the mobile app, users can assign tags to tools by taking a picture. AI software recognizes the object and automatically names it based on its shape and features. Tools can also be renamed manually and categorized by project, location, or worker.
The AI tracks how often a tool is moved, how long it stays in storage, and when it was last seen. This helps teams monitor tool usage patterns, improve storage habits, and predict when tools need maintenance or replacement. Tools that are frequently used or moved can be placed closer to access points. Tools that are idle can be reallocated to other teams.
Toolcase supports multiple users. Team members can view inventory data, receive alerts, and manage the tool database. This improves transparency and reduces the reliance on a single person to maintain records. Team leads and supervisors can assign tools to workers, check inventory remotely, and review tool history for audits or reports.
Inventory data is stored securely within the mobile application. It includes a tool photo, assigned name, RFID tag ID, location history, and status. Tools can be filtered by presence, activity, or category. This system replaces spreadsheets, barcode systems, and manual logs with a streamlined platform built for real-time use.
Toolcase also supports other brands' tags. If a user has pre-tagged equipment, such as Dewalt® Tool Connect™ batteries or third-party RFID stickers, the Toolcase reader can scan and incorporate them into its database without any special configuration. This lowers the entry barrier and allows companies to transition from other tracking systems without replacing existing tags.
A Smarter Way to Work, From Setup to Closeout
Toolcase improves job site operations by giving teams a simple way to control their tools at all times. It works from the start of the workday until the truck is loaded to leave. Setup takes minutes, and adding new tools to the system is fast and automatic. Workers no longer need to check lists or mark items manually. The system handles scanning, alerts, inventory, and location tracking with minimal input.
For job sites with high movement, shared equipment, or frequent location changes, Toolcase prevents common problems that delay progress and increase costs. It reduces the risk of forgotten tools, stops duplicate purchases, and helps maintain job site accountability. With its reliable build, RFID precision, and AI automation, Toolcase provides a secure and effective solution for anyone managing tools across multiple environments.
Comments